Visit Eibach's
web site,
eibach.com
|
|
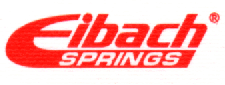
Eibach Springs
by Paul Haney
A car needs springs to isolate the occupants from road irregularities
and maintain tire/road contact. The springing medium can be steel,
air, fiberglass, or anything that contributes a predictable and
repeatable force as the spring deflects through some wheel travel.
Most early automobiles used flat-steel, multi-leaf springs
because they were easy to make and had some interleaf friction
built in that helped damp out unwanted oscillations. Some manufacturers
added friction dampers as in the photo above. A few manufacturers,
mainly Porsche and Chrysler, used torsion bars. Air and rubber/air
hybrid springs have been tried also, but the most popular type
of spring for both racecars and road vehicles is the steel, helical-coil
spring
Because a mass attached to a spring tends to oscillate, a
damper is required, and a helical coil spring with a damper mounted
inside is a compact package. This, of course, is the familiar
"coil-over" spring/damper unit that is widely used
in road cars and all but universal in racecars.
We see coil-over spring/damper units in road racing applications
on both open-wheel and stock-bodied racecars. Springs designed
for use in coil-over applications come with inside diameters
of 2.0 inches, 2.25 inches, and 2.5 inches. Off-road racers use
3.0-inch springs. Some oval-track stock cars, including NASCAR
racecars, use bigger coil springs of 5.0- or 5.5-inch diameter.
NASCAR rules do not allow damper mounting inside the coil spring.
Spring Basics
A spring provides a predictable force for a given deflection.
That force, called the spring rate, is expressed in pounds of
force per inch of deflection: 200 lb./in. In conversation the
inch is generally understood, and racing people talk about "200-pound
springs" or "thousand-pound springs."
A coil spring is really a torsion spring--the wire twists as
the spring compresses. The material's reluctance to twist is
what supplies the resisting force. A common misconception is
that a coil spring "sags" losing spring rate over time,
but a look at the components of the equation for the spring rate
of a coil spring will show you that is not likely if the spring
is properly designed.
Spring Rate = F/S = Gd4/8ND3 where:
F = spring force.
S = spring deflection.
G = torsional modulus of the material.
d = wire diameter.
N = number of active coils.
D = mean (average) coil diameter.
If we peer at this equation a little closer we can figure
out some basic characteristics of coil springs. Look at the variables
that are on the top of the division sign on the right side of
the equation--G and d. Those are the variables that, as they
get bigger, increase the spring rate. G, the torsional modulus,
is a property of the steel used, meaning spring manufacturers
should use the highest-quality steel and heat treat it properly
and consistently.
Because d, the wire diameter, is raised to the fourth power a
small change in this dimension dramatically changes the spring
rate. Since we want all the coils to deflect a predictable distance,
precision springs have to be made from wire that has a constant
diameter along its length.
Look at the spring rate equation again and notice the variables
below the division sign--N and D. These characteristics make
the spring rate decrease as their values increase. A larger number
of active coils and coils wound to a bigger diameter lower the
spring rate. The number 8 comes from the basic geometry of a
helical coil spring and is a constant for all springs of this
type.
Having said that springs can't sag, it is possible if the spring
was designed poorly. If a spring is designed (usually to lower
costs) with marginally small wire or too few coils, and the spring
is fully compressed, the material can be stressed beyond its
elastic limit. The material doesn't fully recover fully when
the stress is removed. Over time, as the underdesigned spring
is repeatedly overstressed, permanent deformation can build up.
Eibach Springs, page 2 |